News
The 3rd Propylene Oxide Industry Chain Technology Development and Industry Development Forum Held at Regular
Experts answer questions on site
Planning Practice Path Looking to the Future Vision
Wang Xiaoyun, Deputy Secretary of the Party Committee of China Chemical News:This year is the closing year of the "13th Five-Year Plan" and the "14th Five-Year Plan" will soon be ushered in ". At present, the petrochemical industry is in a critical period of transformation and upgrading. We believe that to explore the development of epoxy propane industry chain, we should focus on the country to vigorously promote high-quality development, build a "double cycle" new pattern of strategic considerations. Propylene oxide, as a petrochemical product encouraged by the state, with the localization of production processes and the acceleration of large-scale application, the rapid expansion of industry production capacity and the continuous emergence of innovative achievements.
BecauseTherefore, standing on the commanding heights of the industry development, closely linked to "technological innovation and green development" has become the two major concerns of this forum. The forum will focus on advanced production technology, especially co-oxidation and hydrogen peroxide direct oxidation and related supporting technologies in the industrial chain, and discuss the technology and economy of the new technology, as well as the progress of hydrogen peroxide technology supporting HPPO method. Exchange the operation experience of new projects, analyze the development trend of polyether and polyurethane industries, discuss the growth potential of downstream markets such as PPC plastics and propylene glycol ether, so as to promote the technological progress and sustainable development of upstream and downstream industrial chain of propylene oxide industry and expand the market development.
Chairman of Changzhou Ruihua Chemical Engineering Technology Co., Ltd. Xu Zhigang:Organic peroxide technology in China is basically monopolized in the hands of multinational companies. They not only provide technology licensing, often also seek holding cooperation, device development. After years of hard work, Ruihua Chemical has developed a set of technologies that can be licensed and have complete intellectual property rights, which has a great role in promoting the development of the industry. At present, many petrochemical companies have a strong interest in this technology, and two large companies are already implementing production, and the device will enter the chemical production stage from the end of this year to the end of next year.
I wish the propylene oxide industry will make greater progress during the 14th Five-Year Plan period. By 2035, the propylene oxide industry will return to the top of the world in terms of industrial scale, product quality, quality and cost.
Wu Fei, Deputy General Manager of Changzhou Ruihua Chemical Engineering Technology Co., Ltd:As we all know, the traditional technology of propylene oxide production, although the chlorohydrin method is mature and the investment is small, but the pollution is serious. For every ton of propylene oxide produced, about 40-50 tons of saponification wastewater and 2-4 tons of waste residue are produced. These wastes are difficult to treat and costly, causing serious environmental impact. In contrast, the indirect oxidation method can solve the disadvantages of serious waste pollution, equipment corrosion and the need for chlorine in the chlorohydrin method, and can produce a large number of co-products, its industrial process is long, the device investment is large, and it has good economic benefits. Therefore, in the "Industrial Structure Adjustment Guidance Catalog" issued by the National Development and Reform Commission, "200000 tons/year and above co-oxidation propylene oxide plant" is listed as an encouraged project.
Ruihua's isobutane co-oxidation process employs a reaction network of isobutane oxidation, propylene epoxidation and tert-butanol dehydration. Compared with the traditional ethylbenzene oxidation, pure oxygen is used as the oxidant, the decomposition reaction order is higher, the activation energy is closer to the oxidation reaction activation energy, the decomposition reaction is more significant, and the selectivity is higher. At present, the reactors of each step in the reaction network have the characteristics of safe process, simple operation and low environmental risk. Ruihua's independent catalytic technology and epoxidation process design have also improved the whole process based on the enterprise's own requirements.
At present, Ruihua's isobutane co-oxidation process has achieved plant scale and material balance. At present, the method produces 280000 tons of propylene oxide and 550000 tons of isobutylene per year, and the energy consumption is reasonable. The produced isobutene has high purity and low impurity content, and has good economic prospects.
Sun Jie, Deputy General Manager of Jiangsu Yida Chemical Co., Ltd:At present, the HPPO technology independently developed by Yida has completed the research and development stage, and is about to be put into production and show its competitiveness. This competitiveness reflects three aspects, namely, the economy of investment, the advancement of technology and the integrity of technology.
First of all, look at the economy of investment, which is an important aspect for enterprises to enhance their competitiveness. We compared various propylene oxide technologies at home and abroad. Yida's HPPO technology has the lowest investment, with a 300000-ton project investment of about 1.6 billion yuan (excluding investment in raw hydrogen peroxide).
The second concern is the advanced technology. In Yida HPPO technology, the material consumption index of propylene is 0.763 and that of hydrogen peroxide is 0.66. In terms of energy consumption, the energy consumption of 3.1 tons of steam (including by-product recovery) is lower than that of foreign technologies. Electricity consumption is also relatively low. Yida's product quality exceeds the national standard of superior products, and the purity can exceed 99.98%. Yida by-product production is less, is half of similar foreign technology.
The third concern is technical integrity. Yida technology is a complete set of technologies including key equipment such as hydrogen peroxide, catalyst and reactor, reaction process, purification and impurity removal, by-product recovery and sewage treatment.
In September this year, Yida and PetroChina Jilin Chemical Engineering Co., Ltd. jointly completed the preparation of a 300000-ton/year and a 400000-ton/year process package. Our HPPO has officially entered the stage of large-scale industrial development.
Sinopec Refining and Chemical Engineering (Group) Co., Ltd. Luoyang Technology Research Institute Professor Senior Engineer Wei Xiaobo:Continuous flow ionic liquid catalytic hydrogen peroxide propylene oxide production of propylene oxide technology, Luoyang Institute around the research and development center microreactor and process technology research and development platform to develop green propylene oxide production technology, with the international leading level. The technology uses a new type of ionic liquid catalyst developed by East China University of Science and Technology, and is proposed to be developed by Sinopec Refining and Chemical Engineering Group Company Shanghai Engineering Company.
The technology will be a global original propylene epoxidation technology with independent intellectual property rights. After successful development, this technology will be an internationally leading technology. It will be composed of East China University of Science and Technology, SEG Luoyang Technology Research and Development Center, engineering design units, and industrial test applications. All parties will share intellectual property rights in accordance with the technical agreement. rights. If the project development is successful, the application prospect is very good. The peroxyacid salt ionic liquid catalyst used in the process is used for liquid HPPO homogeneous reaction, the oxidation reaction activity is high, and the catalyst and product are easy to separate after the reaction. In addition, the ionic liquid catalyst has the characteristics of high stability (decomposition temperature is greater than 150 ℃), and can efficiently catalyze the epoxidation reaction of various alkenols and olefins under extremely mild conditions (0 ℃ to 60 ℃). This route can solve the difficulties of heat extraction of solid TS molecular sieve catalyst and frequent regeneration of catalyst, and the industrialization of this technology can be realized through microreactor. Catalyst and solvent can be recycled, catalyst replacement and regeneration is very easy.
The experimental results show that the catalyst used in the process has good thermal stability and high product purity. In the future, we will strive to achieve technical goals such as hydrogen peroxide conversion rate of 98%,PO selectivity of 99%, yield of more than 90%, and catalyst life of more than 6 months, and strive to complete medium-sized tests and complete technical application in 2022.
Supporting coordination should ensure both quality and quantity.
Shen Chong, deputy director of hydrogen peroxide technology development department of Liming Chemical Research and Design Institute Co., Ltd:The HPPO process has high quality requirements for hydrogen peroxide. However, industrial hydrogen peroxide usually contains a certain amount of impurities of organic matter, metal ions and their salts. These impurities will deposit or adsorb on the active surface and pore of the TS-1 catalyst, and easily generate ring-opening by-products under acidic conditions, resulting in a decrease in catalyst selectivity. At present, there are technical indicators for the content of organic carbon and phosphate of hydrogen peroxide in China, but the content of alkali metal, alkaline earth metal and anion has not been detected. The influence of raw material hydrogen peroxide quality on HPPO process and PO product quality is unknown.
Liming Institute uses the anthraquinone method to produce hydrogen peroxide, which is the founding enterprise of this method, and this method is also the only industrialized hydrogen peroxide production method at present. At present, the Liming Institute adopts an improved second-generation technology, using a high-efficiency palladium catalyst fixed-bed hydrogenation process, thereby improving hydrogen efficiency and production scale. A number of devices using the production technology of Dawn House.ScaleIt has reached 300000 tons/year.
At present, Liming Institute has a number of different hydrogen peroxide technology, the project investment, production costs, product quality requirements are different, the device operation is safe and stable. According to the requirements of the enterprise, Liming Institute relies on its own research and development strength to design a number of different solutions. The high-yield TBU three-solvent working fluid system has high hydrogen efficiency, large production capacity, good product quality and stable and safe device, the new high-efficiency palladium catalyst is less loaded, less investment, high hydrogen efficiency, large production capacity, low palladium loss, low EAQ consumption, long catalyst life, combined use helps enterprises to reduce costs and increase efficiency. Vacuum dehydration, alkali tower regeneration, clay bed regeneration system to ensure low water content in the working fluid, high regeneration efficiency of degradation products, stable working fluid components, safe and stable device. This in turn ensures the stringent quality requirements of the HPPO process hydrogen peroxide.
Shen Xiaoyan, China Business Manager of Solvay Investment Co., Ltd:Solvay is a global leader in the production of peroxides, a green product in increasing demand. On the basis of peroxide production, Solvay also has the world's most advanced HPPO production process.
At present, Solvay has three single units with an annual output of more than 300000 tons in the world. They are located in Antwerp in Belgium, Mata in Thailand and Dubai in UAE. They all adopt the form of upstream and downstream cooperation. Solvay is responsible for the hydrogen peroxide part and the partners are responsible for the propylene oxide operation, but the technology comes from Solvay. The Antwerp plant is Solvay's first HPPO production unit in the world and was put into operation in 2008. The Thailand unit was commissioned in 2011, while the Dubai unit was commissioned in 2017. The three sets of mature technology and operation all benefit from Solvay's expert team. From design engineering to project management, technical management, process management and operation, the whole team comes from the company.
Solvay device is safe and reliable in operation, large-scale device has no safety accident record for more than ten years, internal OEE efficiency is continuously maintained at 98-99%, and product quality has more than 10 years of performance verification. The plant has a compact design, a small footprint compared to other solutions, low steam power consumption, biodegradable wastewater and no solid waste discharge. Under the same safety and environmental standards, the cost is lower.
Strengthen the support of science and technology to help industrial development
Li Yiming, Project Manager of Beijing Branch of China Huanqiu Engineering Co., Ltd:China Huanqiu Beijing Branch carried out overall design, basic design, detailed design, procurement technical services and on-site technical services for the 270000 tons/year propylene oxide and 600000 tons/year styrene monomer projects of Zhejiang Petrochemical Co., Ltd.
The project has the characteristics of long process flow, complex process and various process units of PO/SM plant. In terms of equipment quantity, the plant includes more than 700 sets of towers, reactors, heat exchangers, air coolers, tanks, pumps, compressors, industrial furnaces, etc., with a large quantity. Utility consumption is also large, including high-pressure steam, circulating water, instrument air, nitrogen, power consumption, etc., with a large number of IO points, and the flare emissions are large, need to set up a separate oxygen flare system. Based on these characteristics, and considering that this is the first engineering application of the 270000-ton PO scale, the company has professionally designed the reaction device and equipment. And organized a number of special expert meetings, organized various relevant professional personnel and company experts to discuss and solve together.
These design ideas make the design of some devices special. For example, in the aspect of high vacuum condenser, due to the high operating vacuum degree of the second coarse tower condenser, the allowable pressure drop is small, and the conventional design may have vibration, large pressure drop and does not meet the process requirements. To this end, the company specializes in optimizing the design, by changing the heat exchanger type and nozzle feed orientation, increase the baffle. It is very good to solve the sound vibration and mechanical vibration in operation, not only the pressure drop is small, but also the uniform fluid distribution also improves the heat transfer effect. The actual pressure drop is reduced to less than 2KPa, the equipment investment is reduced by 32.7, and the heat transfer effect is increased by 41.8. For other specific processes such as the support type of the secondary concentration tower and the comparison and selection of air cooler schemes, the company has come up with targeted professional designs.
At present, the basic design of the project package has been completed, and the detailed design is expected to be completed in August next year.
Tan Xi, Manager of Market Development Department of Xiangyang Hangli Electromechanical Technology Development Co., Ltd:"Safety, high yield, consumption reduction, energy saving, emission reduction" is the eternal theme of chemical plant production management, they also gave birth to the development and application of various related new technologies. Xiangyang Hangli Electromechanical Technology Development Co., Ltd. has successfully developed a turbine refrigeration power generation system that integrates consumption reduction, energy saving, emission reduction, and efficiency enhancement functions, and has successfully operated in the exhaust gas treatment of domestic chemical plants. At present, the turbo expansion refrigeration produced by Hangli The unit and the turbine refrigeration power generation system have been applied to the installations of more than 130 chemical companies at home and abroad.
The traditional system has the problem that the pressure contained in the exhaust gas can not be fully recycled. The work done by the exhaust gas through the shaft is only used for braking at the compressor end, which does not produce benefits. Therefore, how to make maximum use of the residual pressure of the exhaust gas and convert the emitted energy into benefits has become the point of research and development. To this end, "Aviation Electromechanical" has developed two different structures of the expander coaxial direct high-speed power generation and coaxial deceleration power generation system, and has been successfully operated on the chemical production device, to achieve the refrigeration power generation at the same time, complete the exhaust gas residual pressure energy conversion and utilization.
In the upgraded expansion refrigeration power generation grid-connected integrated machine system, the design principle is to ensure the refrigeration function as the premise, to maximize the amount of cold to condense aromatics or other condensable solvents, while recycling the shaft power to generate electricity.
Turbine refrigeration power generation system is a set of refrigeration, power generation functions as one of the energy-saving emission reduction equipment. At present, the exhaust gas flow rate of a single unit is 5000-65000N.m³/h, tail gas pressure 0.1-10MPa, a single unit can generate up to 2MW. The product uses the residual pressure expansion of chemical exhaust gas to do work, in the refrigeration exhaust gas condensation recovery of organic matter at the same time, power generation grid-connected for self-use, to achieve double income. by 20000Nm³/h hydrogen peroxide tail gas as an example, the use of expansion refrigeration power generation system can save 95% of refrigeration power consumption, energy-saving power generation 260KW.
Ding Leijiang, Senior Account Manager of Yououbi Global Oil Technology Co., Ltd:The production process of propylene oxide is varied, and the industrial wastewater produced is not the same. The existing treatment process has a large number of salt-containing wastewater output, which is characterized by high salt, high organic matter and high calorific value organic waste. These contaminants are very difficult to deal with in the state of the art. At present, there are about three main wastewater treatment methods, namely, acidic oil-biological oxidation, WAO high-temperature wet oxidation biochemical method and direct high-temperature thermal oxidation method. Among them, the direct high-temperature thermal oxidation method currently used has some problems. For example, where the molten salt contacts, it can cause corrosion problems, such as in the vicinity of a salt-containing waste water nozzle, and cause partial channel blockage.
To this end, Youobi has developed a variety of solutions, including new refractory materials, burner structure improvements, CFD flow field design, waste water atomization and flue gas quenching equipment. Among them, the burner structure is improved, so that the burner has no swirl parts, all waste gas waste liquid as far as possible axial in the furnace injection and so on. However, the flue gas quenching and dry slagging scheme prevents local strong corrosion at positions such as molten pool and dissolving tank, and the lining salt is accumulated burned through linear combustion to reduce corrosion. Finally, the boiler fouling is weakened and the ash is easier to be cleared.
Yang Chunhe, Technical Director of Sinopec Nanjing Engineering Co., Ltd:Ethylbenzene co-oxidation of propylene oxide produces propylene oxide co-production of styrene (POSM), usually ethylbenzene is oxidized by air at a certain temperature and pressure to ethylbenzene hydrogen peroxide, and then ethylbenzene hydrogen peroxide is used to epoxide propylene to produce propylene oxide, co-production of styrene. However, ethylbenzene oxidation reaction pressure is not high, the reaction is exothermic reaction, the reaction process will release a lot of heat. At low pressure, part of the ethylbenzene vaporizes, taking away part of the heat, and the remaining heat needs to be removed by heat exchange to maintain the reaction temperature of the reactor.
In addition, the above ethylbenzene oxidation tail gas contains evaporated ethylbenzene, nitrogen, unreacted oxygen, water, light components, etc., the temperature of the ethylbenzene oxidation tail gas is usually 130-150°C, the pressure is 0.2-0.5MPa, the oxidation tail gas flow is relatively large, the heat content is relatively high, and it is of great significance to effectively recover the heat of the oxidation tail gas.
Sinopec Nanjing Engineering Co., Ltd. designed the POSM project by using the technology provided by Changzhou Ruihua Chemical Co., Ltd. The original technology of oxidation tail gas heat recovery has many defects, such as insufficient recovery, large consumption of steam and water, etc. After using the new technology process, the heat recovery effect has been greatly improved: the light components and water in circulating ethylbenzene are not easy to be brought into the oxidation reactor, reducing slagging and prolonging the operation period of the device; Before circulating ethylbenzene enters the ethylbenzene oxidation reactor, it is directly mixed with oxidation tail gas for heat exchange, and the heat recovery of oxidation tail gas is sufficient; The amount of heating steam before circulating ethylbenzene enters the ethylbenzene oxidation reactor is small; The oxidation unit has strong adaptability; the tail gas heat exchanger is canceled, the heat exchanger is liquid heat exchange, the heat transfer coefficient is large, the heat exchanger area is small, the consumption of circulating cooling water and preheating hot water is low, the total benefit is to optimize the oxidation conditions of ethylbenzene, the energy recovery efficiency of the oxidation tail gas is high, and the consumption of public works is small. This system is very suitable for large-scale plants, and it is possible to further optimize the subsequent ethylbenzene recovery process, shorten the process and further reduce energy consumption. The energy consumption per ton of styrene products of the new technology is reduced by 9.802kg of standard oil compared with the existing technology, and the energy consumption per ton of propylene oxide products of the new technology is reduced by 24.5kg of standard oil compared with the existing technology. The new technology 200000 tons/year styrene co-production 80000 tons PO, the annual economic benefit is about 12.492 million yuan, if used for 600000 tons/year styrene co-production PO, the annual energy saving benefit exceeds 37 million yuan.
Exploring new paths to empower industry transformation and change
east china university of science and technology professor zhou xinggui:At present, the four main methods of producing propylene oxide have their defects, and the new technology of PO production with environmental protection, energy saving and low cost has its great demand.
In 1998, Japan reported propylene oxyhydrogen epoxidation of propylene oxide, and developed the first generation of gold-titanium catalyst. In 2012, gold-isolated tetravalent titanium catalyst was reported. This catalyst has high activity, good selectivity, significantly improved propylene oxide formation rate and high reaction selectivity. It is equivalent to the activity and selectivity of industrial ethylene epoxidation methods, and basically meets the requirements of industrial production for the space-time yield of the catalyst. The method has other advantages, it uses a one-step reaction, can use a fixed bed reactor, small investment, no solvent in the reaction process, the product and raw material boiling point difference, easy to separate, reaction temperature in 180-220 degrees C, reaction heat can produce medium pressure steam for product separation. If it can be industrialized, it is an environmentally friendly and economical process.
However, the current approach has some drawbacks. In terms of catalysts, there are also disadvantages of difficult to balance conversion and selectivity, low hydrogen efficiency and poor stability. There are many side reactions and the mechanism is complicated. Current frontier research focuses on improving catalyst deactivation, reaction kinetics, and explosion limit prediction.
dalian university of technology professor guo hongchen:Propylene oxide industry is entering a new stage of development, in our country, the diversification of technology is taking shape. Propylene and molecular oxygen phase epoxidation technology is also an important ethylene oxide synthesis technology. In Dalian University of Technology, this work has been done since 2002, and it has been nearly 20 years now. Its reaction conditions and atmospheric reaction temperature and molecular oxygen gas phase method, at 100~200 ℃, the hydrogen peroxide in the form of gas to the reactor, and propylene fully mixed reaction. In theory, this reaction is relatively simple and efficient.
At present, the gas phase epoxidation process is still in the basic research stage. As a premise, we first carried out basic research on the liquid phase method, focusing on the active site of the catalyst TS-1, the relationship between surface properties and reaction selectivity, trace impurities in the circulating methanol solvent, the adverse effects of trace impurities, and the formation of trace impurities. These are the problems that plague the epoxidation process. The understanding of such work will have some guidance for us to improve the catalyst and reaction process.
Liu Zhun, General Manager of Jiangsu Yida Chemical Co., Ltd:This year, the entire propylene oxide market is in an explosive market, with the highest price reaching 19000 yuan/ton, the highest level since 2008. This price is due to the surge in demand and prices of downstream polyether polyols, which triggered a surge in the price of propylene oxide. I personally understand that it is abnormal for the price to reach 19000 yuan/ton. In fact, the price of propylene oxide has gradually decreased on the basis of 19000 yuan/ton recently. At present, the price of propylene oxide is also around 15000 yuan/ton, but the price of propylene oxide is a more reasonable price at 10000 yuan/ton.
Companies that invest in propylene oxide must invest in propylene oxide projects from the perspective of their own strength and their own raw material advantages, market advantages, regional advantages, etc.
Yang Xianghong, a senior expert in the petroleum and chemical industry:This year we have witnessed history: propylene oxide has set a new high since 2012 and once touched 18900 yuan/ton; since September, production enterprises have maintained an ultra-high profit of more than 9000 yuan/ton; the downstream rise is even crazier, with polyether reaching an 11-year high, and the market price of dimethyl carbonate has broken through 14000 yuan/ton. Although the market price of propylene oxide began to fall, this crazy market has attracted great attention from the chemical industry, because a large wave of frightening new production capacity is on the way.
From the perspective of the industrial chain, the raw material of propylene oxide is propylene, and the excess capacity of propylene is a foregone conclusion. In 2019, my country's propylene production capacity reached 40 million tons/year, and in the future, there will be no less than this number of propylene production capacity is coming. By 2025, China's propylene production capacity will exceed 84 million tons/year. In propylene oxide, due to considerable profits and market demand to attract a large number of new entrants, and to undertake the upstream pressure of propylene, the industry is in an expansion trend. With the increase of import dependence, China's current propylene oxide production capacity under construction exceeds 8.7 million tons/year, and the serious overcapacity of basic propylene oxide is a foregone conclusion. However, in the next five years, the growth rate of global PO market demand will not exceed 3%, and China may reach 4%, which means serious overcapacity and serious homogenization of production products. This almost means that the price war of propylene oxide will break out.
On the downstream side, the industry with the largest number of propylene oxide customers and the largest demand is the polyether polyol industry, while the number of other chemical downstream enterprises is not large and the willingness to expand capacity is not high. Prospects for future expansion in industries such as isopropanolamine, flame retardants, cellulose and additives are also unsatisfactory. In the future, the main consumption growth point of propylene oxide downstream will still be concentrated in the polyether polyol industry. It is expected that the production capacity of polyether polyol will increase to 10 million tons/year in 2025, which can consume 3.45 million tons/year of propylene oxide. However, companies cannot focus their growth points on polyether polyols, but rather on emerging high-end areas such as polyurethanes, surfactants, and polyether amines.
Oriental Securities Senior Analyst Ni Ji:At present, the propylene oxide market is in short supply. The reason for this problem, first of all, is that the three main domestic processes have different aspects of the problem, once affected the expansion of production. After 2015, the growth rate of domestic PO supply decreased significantly. But the demand side has been growing rapidly, even if this year affected by the epidemic, the traditional demand performance is still better, and then superimposed on the mattress anti-dumping and other factors, resulting in domestic epoxy propane phase in short supply, prices soared.
However, the propylene oxide industry is approaching an inflection point. At the technical level, the industry is also good. Co-oxidation technology, which is monopolized by overseas enterprises, is expected to be broken through by domestic enterprises. This has led to the commissioning of a number of co-oxidation production units and a rapid increase in market input, with domestic propylene oxide production capacity reaching 4.7 million tons by 2022, up 38% from the current level, even without considering HPPO production capacity. This will lead to a decline in the industry's average operating rate after 2020. The new co-oxidation method is on the right side of the cost curve, in the case of new demand is not as good as new supply, the industry will enter the tragic right side of the extrusion process.
When it comes to cost, it is necessary to compare the economy of various processes. At present, the cost of chlorohydrin method is continuing to increase, HPPO method is the lowest, co-oxidation law in 2500-3000 yuan/ton. In addition, in terms of profitability, the profitability of the co-oxidation method is the best. Because the HPPO method, although the operating cost is low, but the oxidant is expensive, there is no by-product amortization cost, which restricts its profitability.
Jiangsu Zhongshan Chemical Co., Ltd. Doctor, Senior Engineer Zong Hongliang:Progressive propylene oxide technology affects the future of polyols because it is a high-cost component, and most propylene oxide producers are also major polyether polyol producers, so all changes in the propylene oxide market will directly affect polyol producers and polyol downstream users.
Polyether polyol is a series of polymer compounds containing ether bonds in the molecular chain made of epoxide ring-opening polymerization, which can be divided into three categories according to the polymerization monomer. Among them, polymers obtained by ring-opening polymerization of lower alkylene oxide monomers such as propylene oxide or ethylene oxide with active hydrogen-containing compounds such as polyols or polyamines as initiators are collectively referred to as PPG and are the most widely used polyether polyols.
At present, China's polyether polyol industry has the characteristics of large industrial scale, obvious overcapacity, relatively low technical level, low degree of technical differentiation, serious homogenization of low-end products, fierce market competition and low market share of high-end products.
However, polyether polyols are widely used, soft foam is a common home improvement material, high resilience polyether is used in automobile interiors, and shoe material polyether is widely used in footwear production. Among several high-end polyethers, the foam prepared by slow rebound polyether has the functions of shape memory, energy absorption, sound absorption and shock absorption, and is used as impact absorber, sound absorber and shock absorber. Hard foam polyether is mainly used to prepare rigid polyurethane foam. Elastomer polyether is suitable for polyurethane elastomer, coating, adhesive, sealant, etc.
Polyether polyols are widely used, and China is also the world's largest polyurethane production and consumption area. At present, the industry has entered a new period of development and promotion. High-quality environmental protection and sustainability are its development direction. It can be said that this industry still has many development directions. Take the high-end route, in order to avoid the homogenization of competition.
This forum was co-sponsored by China Chemical News and Changzhou Ruihua Chemical Engineering Technology Co., Ltd., and co-organized by Jiangsu Yida Chemical Co., Ltd. and China Huanqiu Engineering Co., Ltd. Beijing Branch. The number of participants was nearly 200. The forum conducted in-depth discussions around the theme of "technological innovation and green development", presenting a nutritious technological feast for the industry. (Photo: Xue Qinghai Video: Han Jie)
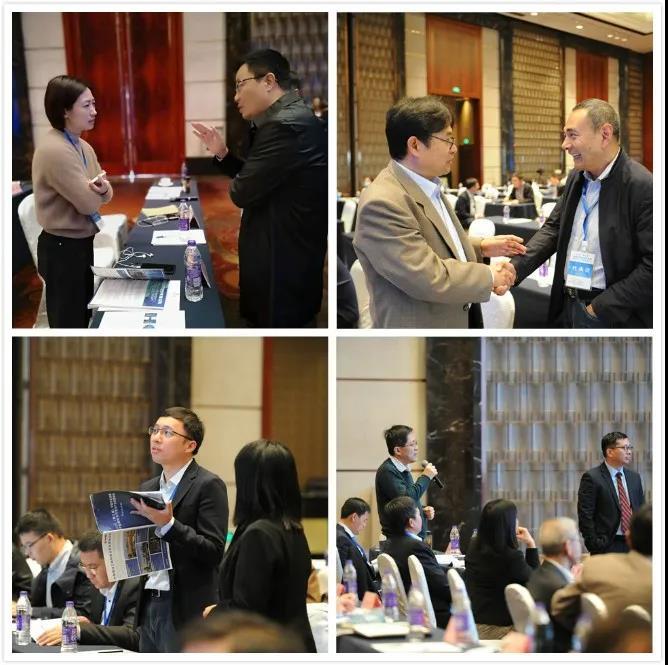
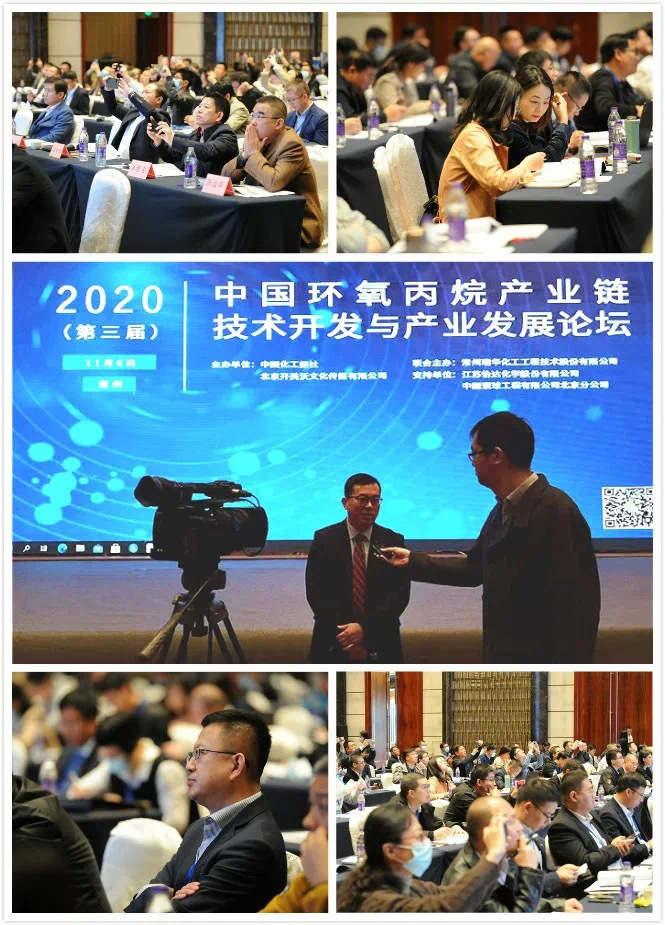
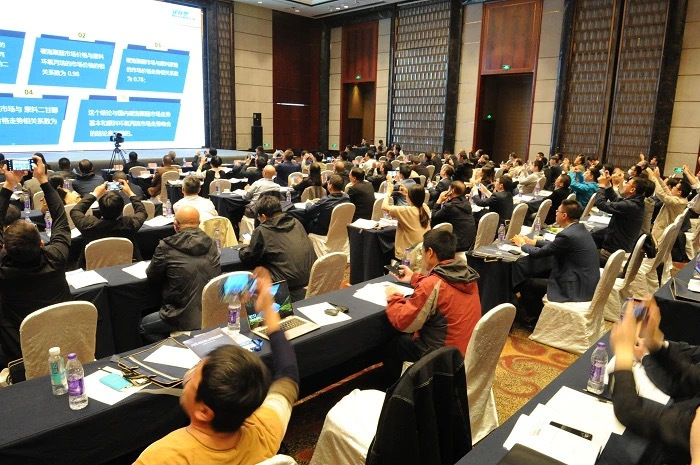
Contact us

5/F, Block A, Building 1, Chuangyan Port, Science and Education City, Wujin District, Changzhou City, Jiangsu Province
Copyright© 2024 Ruihua Chemical