News
2021 China International Petrochemical and Downstream Industry Technology Conference and the 9th International Light Hydrocarbon Comprehensive Utilization Conference
On the afternoon of March 17, at the Degradable Materials Technology Forum 2021 the China International Petrochemical and Downstream Industry Technology Conference and the 9th International Light Hydrocarbon Comprehensive Utilization Conference, the participating experts discussed the preparation, research and development, application and application of various degradable materials. Industrial development trends were shared brilliantly.
BDO roadblocks: calcium carbide raw materials are in short supply, and natural gas law approval is difficult.
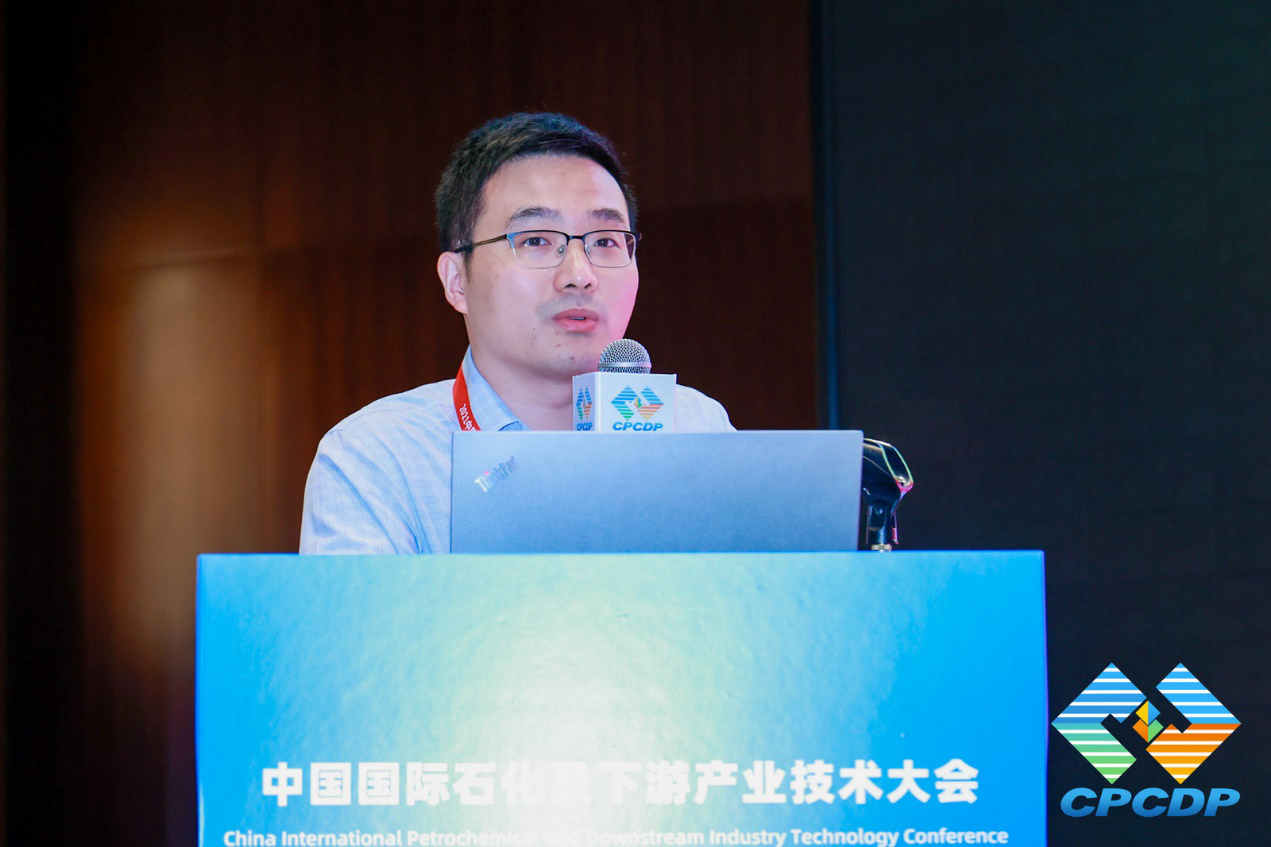
Ni Ji, Chief Analyst of Chemical Industry, Orient Securities Research Institute
Ni Ji, Chief Analyst of Chemical Industry, Orient Securities Research InstituteIt is pointed out that at present, degradable plastics have entered the outbreak period of the industry, and large-scale domestic PBAT projects are also emerging one after another, with a planned production capacity of about 5 million tons/year. With the expansion of supply and the maturity of technology, PBAT prices are also expected to fall further, together with PLA to become an important material for the development of degradable plastics.
The increasing number of new PBAT projects indicates that the product has low technical barriers. Although the short-term profit is better, but if there is no breakthrough in the modification and products, the long-term view will inevitably fall into cost competition, the degree of integration, scale effect, cost control will become the key indicators to measure its competitiveness.
The main raw materials of PBAT are BDO, adipic acid and PTA, in which a large amount of hydrogen (or synthesis gas) is used in the production process of BDO and adipic acid, including methanol and synthetic ammonia synthesis, benzene hydrogenation, etc. The natural gas route is used to produce BDO to match PBAT. The by-product synthesis gas can just meet the hydrogen consumption of adipic acid. Theoretically, as long as there is natural gas, benzene and air (nitrogen and oxygen are provided) at the raw material end, BDO and adipic acid products that meet the requirements of PBAT can be produced.Therefore, the natural gas method BDO has a unique advantage.
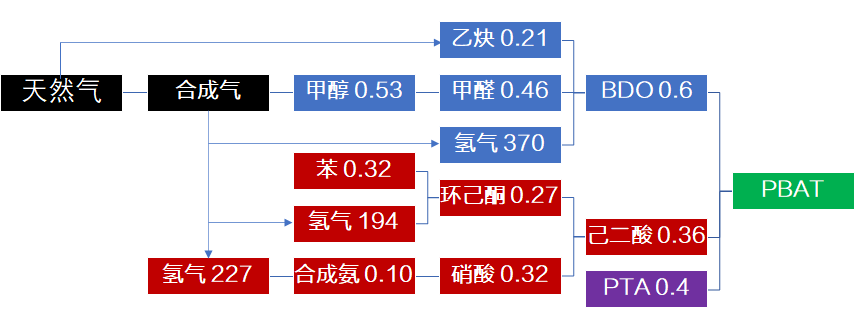
Figure 1 Ton of PBAT Raw Materials
(The number after the product indicates unit consumption: ton, hydrogen unit: square/ton)
However, BDO is subject to calcium carbide shortage and natural gas law approval, which may become the threshold to limit PBAT expansion.
Biodegradable materials will evolve into biosafety materials
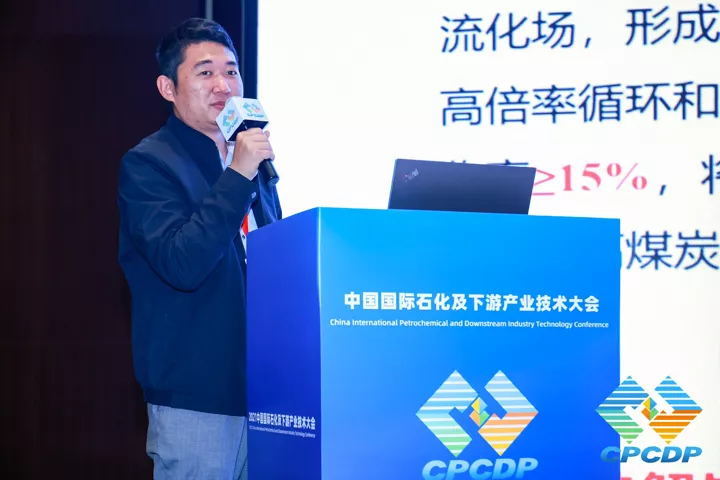
Yang Dongyuan, vice president of Shaanxi Yanchang West University Advanced Technology Research Institute and graduate tutor of Northwest University
(The following only represents the personal views of experts and does not represent any unit or institution)
Yang Dongyuan, vice president of Shaanxi Yanchang West University Advanced Technology Research Institute and graduate tutor of Northwest UniversityIt is pointed out that there are still some problems in the preparation of biodegradable monomers by biological method, such as high cost, uncertainty in the acquisition of large-scale raw materials, food security, and waste discharge,For example, 2.5 tons of corn can get 1 ton of PLA.
Relatively speaking, the preparation of degradable monomers from fossil raw materials has the advantages of low price of large-scale raw materials, abundant and easy access to sources, low cost, significant scale effect, and concentrated pollution emissions,For example, the coal glycol route to PGA, the cost can be close to PE.
Yang Dongyuan said that future materials will evolve from biodegradable materials to biosafety materials.Degradable materials of the future will have three characteristics:
First, affinity to the human body, from biodegradable environment-friendly to bioabsorbable;
The second is integration, from thousands of years of natural degradation to return to the hourly metabolism;
Third, smart materials, from the physical and chemical properties of curing materials to adjustable repair.
Three Directions of Degradable Plastics Modification
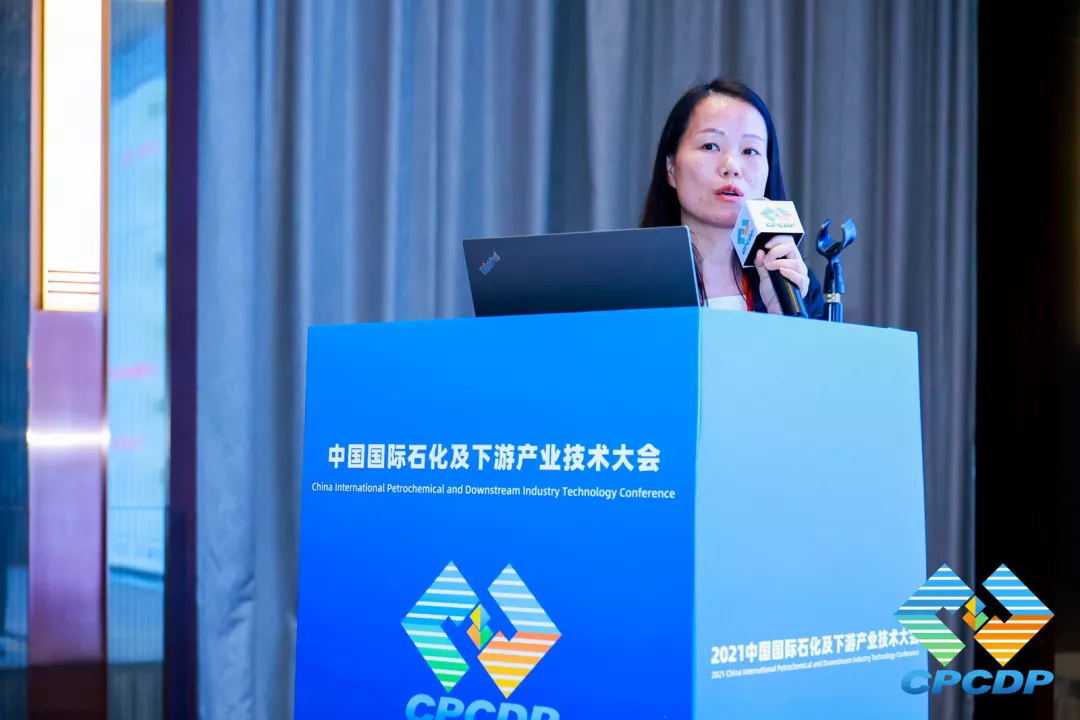
Wang Pingli, Senior Engineer, National Engineering Research Center of Engineering Plastics, Technical Institute of Physics and Chemistry, Chinese Academy of Sciences
Wang Pingli, Senior Engineer, National Engineering Research Center of Engineering Plastics, Technical Institute of Physics and Chemistry, Chinese Academy of SciencesIt is pointed out that the substitution of degradable plastics is an important way to reduce the source of plastic pollution. The modification of degradable plastics has three directions: alloying, cheapening and functionalization.
At present, the demand structure of degradable plastic products is:
● Membrane bags for daily use:The most mainstream products, mature technology, Hainan next year demand 48000 tons;
● Meal box tableware:Rapid development of products, technology needs to be improved, Hainan next year demand 15000 tons;
● Film:The ban covers products, the technology is basically mature, and the price is far from market acceptance;
● Express:Plastic ban covers products, degradation tape to be improved, enterprises are trying to reserve, wait and see the market.
Degradable plastic resin demand structure is:
●Pbat:Mainstream basic products;
●PLA:Mainstream basic products;
●PBS:High-speed development of basic materials;
●PGA/PPC/PHA/PCL:Functional materials.
What kind of polymer materials can be biodegradable
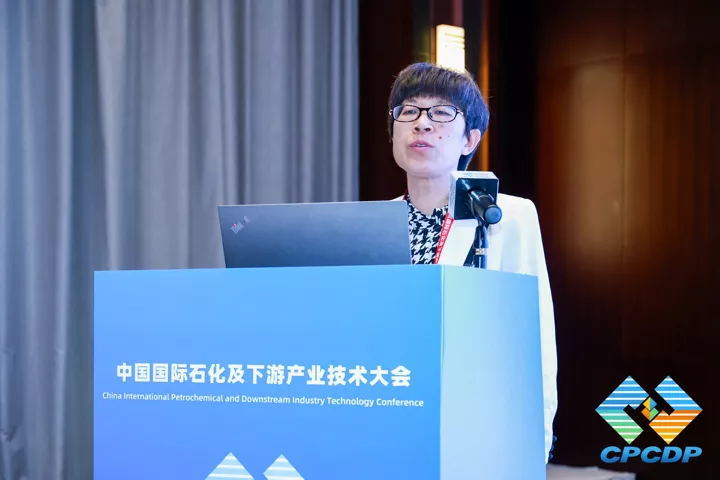
Dai Junming, Senior Expert and Professor-level Senior Engineer of Sinopec Yizheng Chemical Fiber Co., Ltd.
Dai Junming, Senior Expert and Professor-level Senior Engineer of Sinopec Yizheng Chemical Fiber Co., Ltd.It is pointed out that the degradation of biodegradable polymer materials has biophysical and biochemical effects, accompanied by other physical and chemical effects, such as hydrolysis and oxidation, etc.; the degradation depends on the size and structure of the polymer, the type of microorganisms and environmental factors such as temperature and humidity; the biodegradability of different chemical structures is as follows: aliphatic ester bond, peptide bond> carbamate> aliphatic ether bond> methylene; high molecular weight, regular molecular arrangement, hydrophobic polymer materials are not conducive to the erosion and growth of microorganisms, and are not conducive to biodegradation; the length of fragments produced by degradation is proportional to the thickness of the single crystal layer of polymer materials, and the smaller the polarity, the more easily the copolyester is degraded by fungi, and the degradation effect of bacteria on polymer materials with high a-amino content is very obvious.
At present, the mechanism of biodegradation has not been fully studied.
CO2There are 10 ways of resource utilization
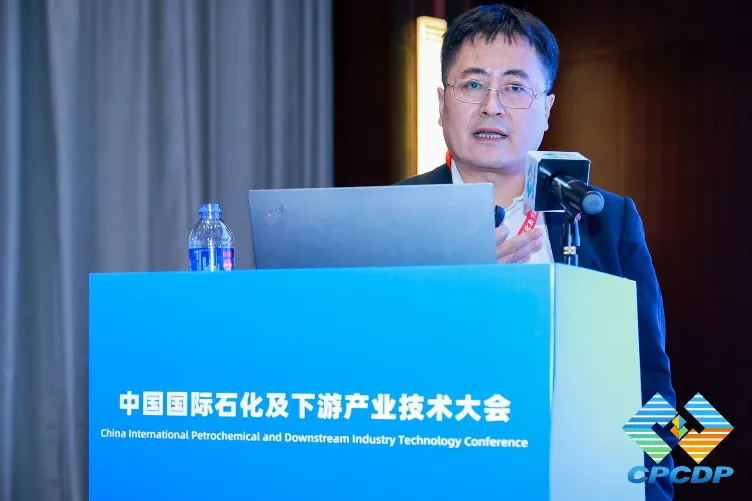
Dr. Kong Fanzhi, Vice President of Innovation Institute of Oak Holding Group
Dr. Kong Fanzhi, Vice President of Innovation Institute of Oak Holding GroupIt is pointed out that there are 10 ways to utilize CO2 as a resource: ① to produce chemicals from CO2; ② to produce fuels from CO2; ③ to use microalgae for biotransformation; ④ to be used as a concrete building material; ⑤ to enhance oilfield regeneration (CO2-EOR);⑥ to enhance bioenergy from carbon capture and storage (BECCS);⑦ to enhance weathering; ⑧ to include forestry technologies for afforestation and reforestation; ⑨ Land management through soil carbon sequestration techniques; ⑩ Biocarbon.
Ethylene carbonate (EC) and dimethyl carbonate (DMC), as polar aprotic solvents with high boiling point, are used in industry as lubricants, electrolyte solvents for lithium ion batteries, synthetic modules for polymer materials, comonomers for polycarbons and synthetic intermediates for other fine chemicals.
Oak Holding Group has successfully produced ethylene carbonate (EC) and dimethyl carbonate (DMC) from CO2.
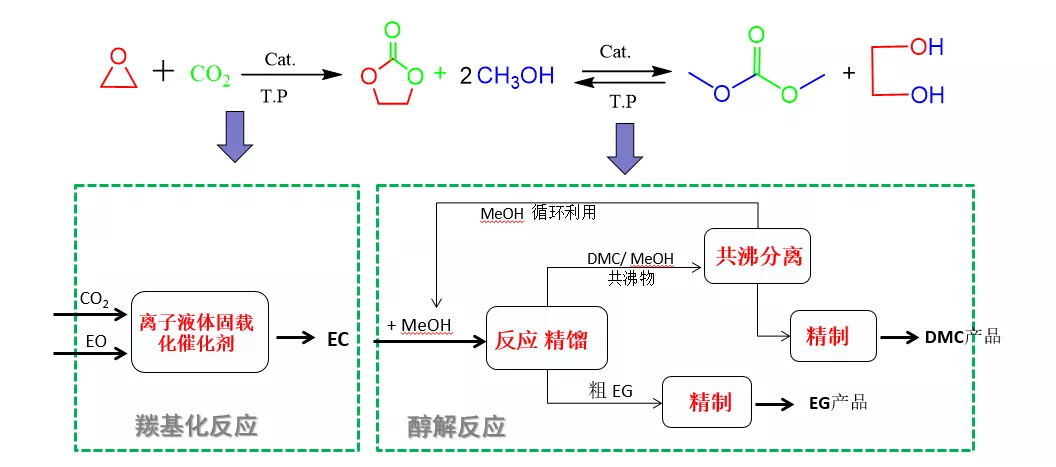
Oak EC/DMC Process Flow Diagram
The Oak-Process EC/DMC process has three breakthrough core technologies:
One is the ionic liquid hydrogen bond strengthening reaction and chemical immobilization;
Second, gas-liquid efficient distributed tube reactor design;
Three is the reaction distillation coupling and the whole process of energy saving optimization design.
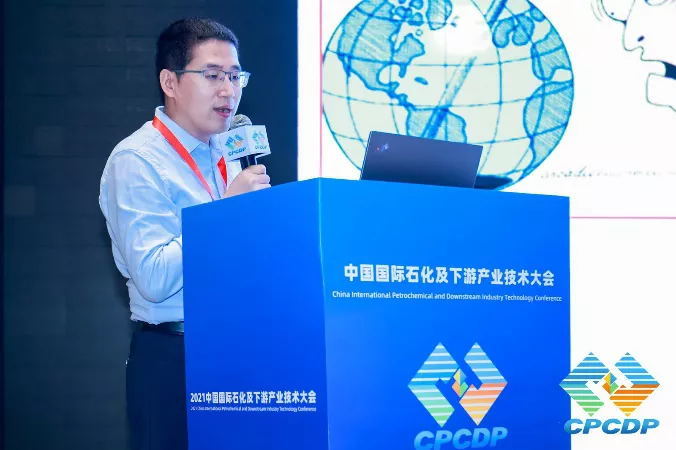
Han Changyu, Researcher, Changchun Institute of Applied Chemistry, Chinese Academy of SciencesThe development and market application of biodegradable material products are introduced.
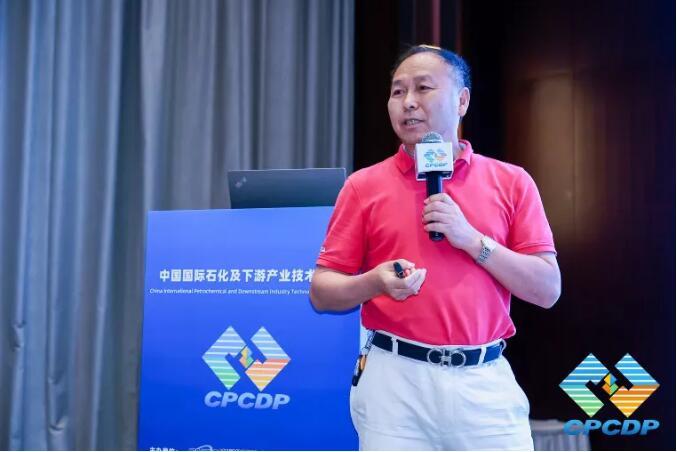
Meng Yuezhong, Distinguished Professor of "Pearl River Scholars" in Guangdong Province, Second Class Professor of Sun Yat-sen University, Director of Guangdong Key Laboratory of Low Carbon Chemistry and Process Energy ConservationA new type of biodegradable carbon dioxide based semi-aromatic copolymer is introduced.
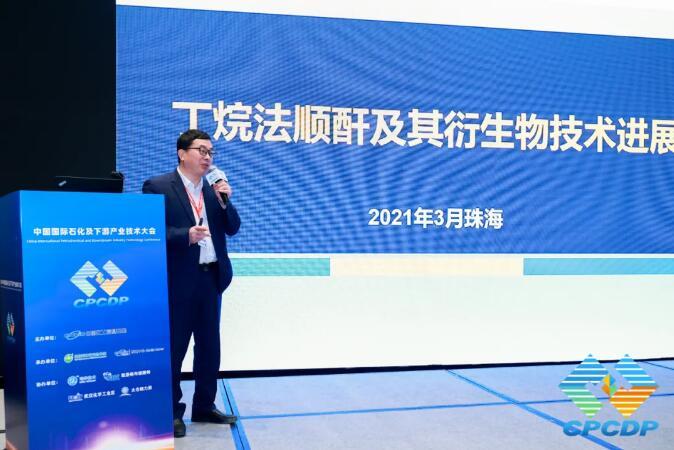
Chairman of Changzhou Ruihua Chemical Engineering Technology Co., Ltd. Xu ZhigangMaleic anhydride is one of the world's three major anhydride raw materials (acetic anhydride, maleic anhydride, phthalic anhydride), and its downstream products have a wide range of development and application prospects, can be used in synthetic resins, coatings, pesticides, lubricating oil additives, pharmaceuticals, paper treatment agents, food additives, stabilizers and so on. At present, the production technology of maleic anhydride mainly includes butane process and benzene process. At present, the production capacity of maleic anhydride in China is mostly the traditional benzene process, but with the promotion of the utilization of carbon four resources, the butane process maleic anhydride device has gradually formed a scale. Ruihua maleic anhydride technology uses n-butane as raw material and reacts with air to produce maleic anhydride. The oxidation reaction is a strong exothermic reaction, and the reaction heat needs to be removed during the reaction process, so the maleic anhydride device can output a large amount of steam. Because of this feature, the maleic anhydride device is suitable for joint setting with some high steam consumption devices, such as ethylbenzene styrene device, which can achieve the purpose of steam complementarity and improve the economy of the two sets of devices. Compared with the traditional benzene maleic anhydride technology, RHMA technology can completely eliminate the pollution of benzene to the environment, high yield of maleic anhydride, low energy consumption, high amount of external steam, long operating cycle of the device.
The butane is evaporated and mixed with air before entering the oxidation reactor. The oxidation reactor is a tubular fixed bed reaction type. The catalyst is placed in the reaction tube. Butane and air react to generate maleic anhydride after contacting with the catalyst. At the same time, a large amount of reaction heat is released and removed by the molten salt on the shell side. The heated molten salt is returned to the reactor after being used to produce steam. In the oxidation reactor, the single-pass conversion of butane can reach 82 ~ 85%, and the weight yield of maleic anhydride is 97~103%.
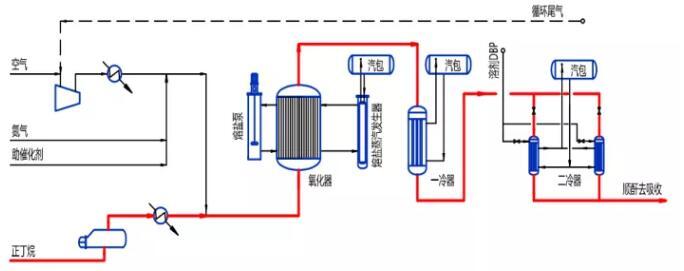
After the reaction, the gas enters the post-treatment system after two-stage cooling. The post-treatment system of Ruihua maleic anhydride technology adopts solvent absorption process, and the solvent is dibutyl phthalate. The reaction gas after absorption, desorption, purification and other operations to obtain the product maleic anhydride, purity of 99.5%.
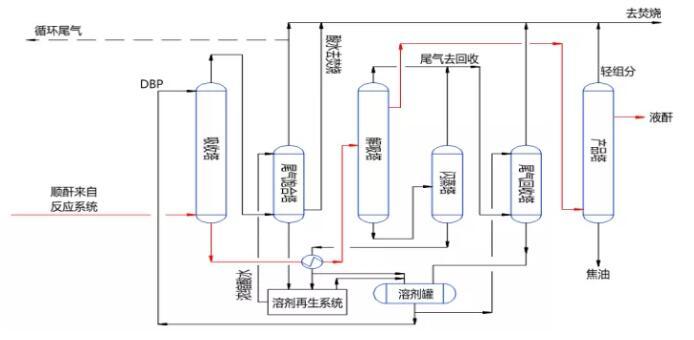
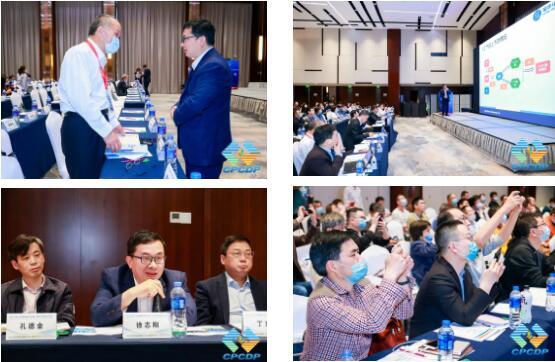
CHANGZHOU RIHUA CHEMICAL ENGINEERING TECHNOLOGY CO., LTD
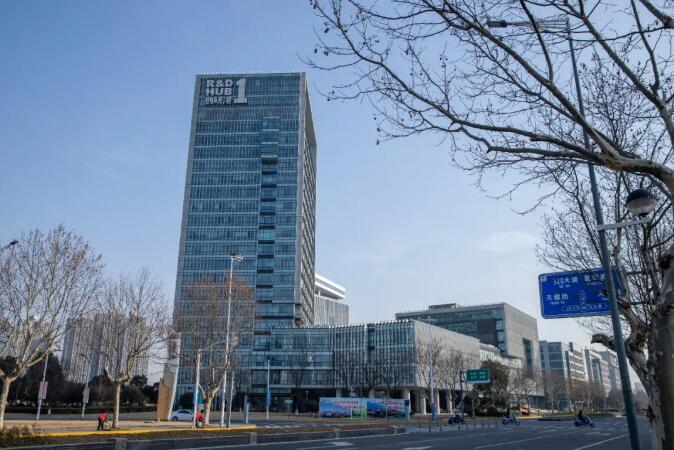
Changzhou Ruihua Chemical Engineering Technology Co., Ltd. was established in 2007 and is located in the Science and Education City, Wujin District, Changzhou City. It is a professional company with a number of patented technologies and is mainly engaged in engineering and technical services in the petrochemical field. The company, formerly known as Changzhou Ruihua Chemical Engineering Technology Co., Ltd., completed the share reform in December 2017 and officially changed its name to Changzhou Ruihua Chemical Engineering Technology Co., Ltd. In July 2018, the new three boards (Ruihua Technology 872869) were officially listed.
Since the establishment of the company, the business has maintained rapid growth. It has established good business contacts with famous large petrochemical enterprises at home and abroad, and has established solid cooperative relations with well-known chemical companies, engineering companies, patent dealers, industry associations, large design institutes and research institutes at home and abroad. As a professional company engaged in engineering and technical services in the field of petrochemical industry, Ruihua Chemical is committed to providing users with comprehensive, systematic and professional engineering services and helping users create more value.
Gathering first-class elite talents, establishing first-class technology base and creating first-class modern enterprises are the goal of Ruihua Chemical, and also the road of development that Ruihua is taking. In addition, the company attaches great importance to the protection of intellectual property rights and has applied for and authorized more than 60 patents.
Contact us

5/F, Block A, Building 1, Chuangyan Port, Science and Education City, Wujin District, Changzhou City, Jiangsu Province
Copyright© 2024 Ruihua Chemical